SENTEZ Optimum Kimya
Sentez Optimum Kimya farklı sektörlerde endüstriyel tutkal ihtiyacı olan firmalara ülke genelinde güvenilir, hızlı, ekonomik ve etkin çözümler sunmak amacıyla 2017 yılında Bursa'da kurulmuştur.
Endüstriyel tutkal sektöründe dünya devlerinden biri olan Jowat'ın bölge distribütörlüğü ile başlayan yolculuğu uygulamaya yönelik olarak daha farklı çözümler sunabileceği farklı markaları da bünyesine katması ile devam etmiştir.
2019 yılından beri kendi formülasyonlarını kendisi gibi üstün kalite anlayışına sahip üreticilerde fason ürettirip SENTA markası ile müşterilerine sunmaktadır.
2021 yılı ile birlikte tutkalın yanında müşterilerinin ihtiyaç duyduğu bazı hammaddeleri de portföyüne dahil etmeye başlamış ve bu kapsamda müşterilerine sunduğu ürün ve hizmetleri çeşitlendirmiştir. Bu yöndeki büyümesine de piyasa ihtiyaçları ve teknolojik ilerlemeler doğrultusunda devam etme kararlılığındadır.
Portföyünde yer alan yapıştırıcılar, sızdırmazlık ürünleri, fonksiyonel kaplamalar ve hammaddeler ile müşterilerine rekabet avantajı ve eşsiz bir müşteri deneyimi vermeye hazırdır. Yaratıcı düşünce ve girişimci ruh firmanın DNA’sının ayrılmaz parçalarıdır.
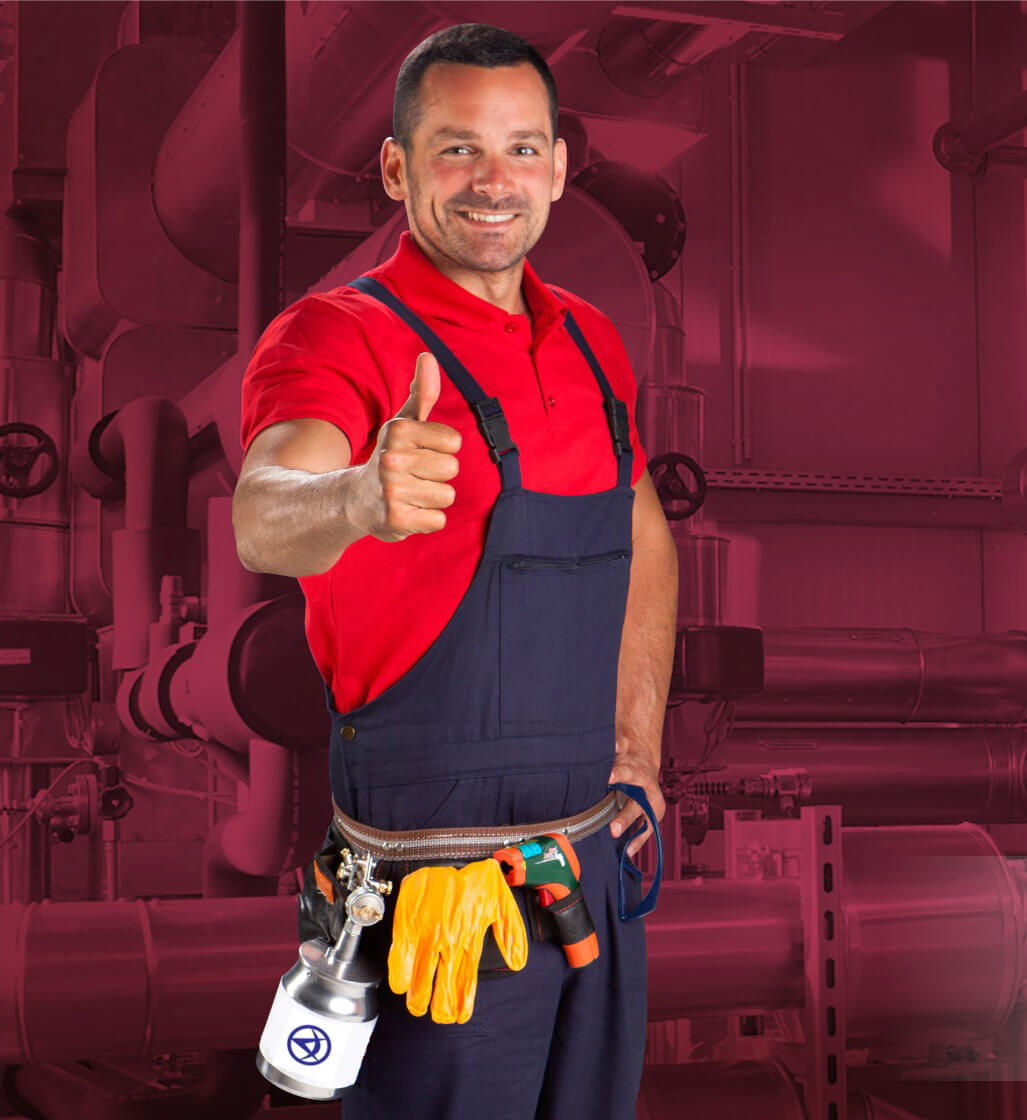